About the Author
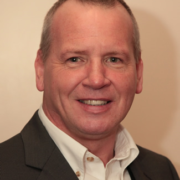
For over 30 years, Martin Robinson has been a pioneer in the field of condition based maintenance technology. He spent 18 years in the British Army specializing in field maintenance of combat fleet vehicles. Mr. Robinson continues to be an innovator and pioneer the technological benefits of Infrared Thermography internationally. He has met with, consulted, or advised international maintenance and reliability leaders on electrical preventive maintenance (EPM) and electrical safety standards of NFPA and OSHA. A recognized authority in the field of Infrared (IR) Thermography, Mr. Robinson has designed CBM programs to include IR, Non-destructive Testing (NDT) and implementation of green energy initiatives and energy management strategies.
Martin holds a NEBOSH certificate in Occupational Safety and Health, a Level III Certified Infrared Thermographer and is also a Certified Maintenance and Reliability Professional (CMRP) through the Society for Maintenance and Reliability Professionals (SMRP). He is also a member of IEEE, NFPA and is a standing member on the technical committee CSA Z463 guidelines on maintenance of electrical systems and a member of the IEEE P1854 working group (Recommended Practice for Electrical System Design Techniques to Improve Electrical Safety).