According to the statistics, there are more than 50 billion bearings being manufactured during the past 5 years around the world. Only a relatively small percentage of all bearings in use fail. Majority (90%) of the bearings outlive the equipment in which they have been installed. About 9% bearings are replaced prior to failure due to preventive reasons. Approximately 0,5% of bearings are replaced because they are broken or fail. This means that around 50 000 000 bearings are replaced every year due to damage and failure. Based on the research, around 1/4 to 1/3 of the total bearing damage or failure are due to lubrication problems, such as wrong lubricant and quantity, wrong lubrication interval etc.
Purpose of Lubrication
The main purpose of lubrication is to reduce friction and wear inside the bearings that may cause premature failure. The effects of lubrication may be briefly explained as following:
- Reduction wear and friction
Metal to metal contact between the bearing rings, rolling elements and cage, is prevented by the oil film which reduces the friction and wear in the contact surface.
- Extension of fatigue life
The rolling fatigue life of bearing depends greatly upon the viscosity and film thickness between the contact surfaces. In normal operation, a heavy film thickness prolongs the fatigue life, but it is shortened if the viscosity of the oil is too low and the film thickness is insufficient.
- Dissipation of frictional heat and cooling
Circulation lubrication is used to take away frictional heat or heat transferred from the outside to prevent the bearing from overheating and the deteriorating of the oil.
- Guard against corrosion and rusting
Adequate lubrication also helps to prevent foreign material from entering the bearing and guards against corrosion and rusting.
Lubrication methods
The basic methods can be divided into two categories: grease and oil lubrication. By adopting the suitable lubrication method for the applications, one can achieve better motion performance of the bearing. A comparison of the two methods can be seen in the table below.
Item |
Grease |
Oil |
Housing structure and sealing |
Easy |
Maybe complex and careful maintenance required |
Speed |
65-80% of that with oil lubrication |
Higher limiting speed |
Cooling effect |
Average to poor |
Heat transfer is possible with oil circulation |
Fluidity |
Poor |
Good |
Lubricant replacement |
Sometimes difficult |
Easy |
Removal of particles |
Nearly impossible |
Easy |
Contamination due to leakage |
Sometimes if over greased |
Often leaks if without proper countermeasures. |
In general, oil offers superior lubrication; but grease lubrication allows a simpler structure design of the bearing. Depends on the operation condition, some major factors such as grease and oil quantity, replacement interval etc., shall be carefully examined to formulate the correct lubrication approach.
Methods for lubrication inspection during operation
- SPM HD
Bearings can only achieve maximum performance levels with adequate lubrication. The lubrication conditions of a bearing should therefore be monitored closely. There are various ways to reveal the lubrication conditions of a rolling element. SPM HD® technology is used for a fast, easy, and reliable diagnosis of the operating condition of bearings. Shock pulse amplitude is basically determined by three factors:
- Rolling velocity
- Lubrication condition
- The mechanical state of the bearing surfaces (roughness, stress, loose metal particles).
HDm
It is the primary value to use to determine the severity of the bearing damage. It represents the highest shock pulses found during the measuring cycle.
HDc
This value represents the level where 200 shocks/second are present. It is useful to determine the lubrication condition.
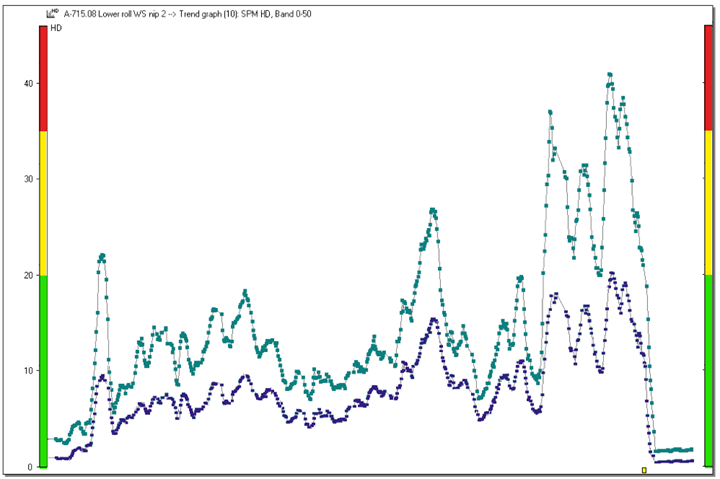
The height of the carpet value and delta (HDm minus HDc) indicate lubrication quality or problems with bearing installation and alignment. All measurements can be easily visualized and evaluated in the scale of green-yellow-red.
- LR/HR and Lubmaster
The LR/HR method was developed from the original Shock Pulse Method for condition diagnosis of rolling element bearings. It allows a precision analysis of oil film condition in the rolling interface and contains calculation models for finding the optimal lubricant.
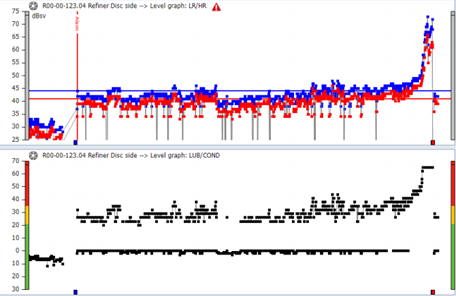
After measurement the measuring device returns
- a general description of bearing condition (CODE)
- a value for oil film condition (LUB)
- a value for surface damage (COND).
A LUB no. of 0 means dry running, the value increases with oil film thickness. A COND no. of around 30 indicates surface stress or early damage, the value increases with damage severity. The general assessment is:
- CODE A Good bearing
- CODE B Poor lubrication
- CODE C Damage in early stage
- CODE D Damage
A program part, LUBMASTER, uses the shock values plus data on lubricant type, viscosity, load, and operating temperature to calculate the bearing’s life expectancy under present condition. It also calculates the effect of changes in oil type and viscosity.
- Temperature & other inspection during operation
It is important to monitor the operating temperature at bearing positions. If the operating conditions have not been altered, an increase in temperature is often an indication of imminent bearing damage. There are different prob or sensors for temperature measurement. However, keep in mind that a natural temperature rise lasting 24 to 48 hours normally occurs immediately after first machine start up and after each re-lubrication when using grease. Other inspection methods could also include the followings.
- Check that automatic lubricating systems are functioning accordingly.
- Check the lubricant level in reservoirs and replenish if necessary.
- Check for lubricant leaks visually.
- Optimize the re-lubricate according to schedule if manual greasing.
- Change oil according to schedule.
- Follow the specified lubricant as per instruction from OEM.
Lubrication inspection during machine shutdown
When a machine is shutdown, there is a chance to assess the condition of bearings, seals, housings, and lubricant. A general inspection can often be done by removing a housing cover or cap. If a bearing appears to be damaged, it should be dismounted and thoroughly inspected. Shaft and belt alignment as well as a thorough inspection of the machine foundation and exterior can also be done during a machine shutdown.
Summary
By applying the right lubricant with right amount in the right time, we can prolong the lifetime of those which failed due to wrong lubrication. Up to 1/3 of the total bearing damage or failure are due to lubrication problems. This means that every year more than 16,000,000 of bearings’ lifetime can be prolonged or extended with the correct lubrication strategy. Meanwhile, condition monitoring technology such as, SPM HD, acceleration measurement and other inspection methods can help us easily reveal the lubrication condition and provide long pre-warning time for correct maintenance actions.