Minimizing contact with dangerous work areas is one of the simplest ways to keep personnel safe. In the past, workers had no choice but to enter dangerous environments and manually collect asset data. Because of today’s connectivity and technologically advanced devices, the need to be physically present to take measurements in potentially dangerous environments or hard-to-reach areas is disappearing.
With the implementation of reliability solutions such as remote condition monitoring sensors, measurements can be recorded from a distance, eliminating the need for employees to enter danger zones. Once placed on an asset, wireless sensors continuously monitor the equipment, and the data is streamed and stored in the cloud. It can then be accessed easily by personnel using a smart device, such as a mobile phone, tablet, or computer. By screening asset performance continuously, reliability professionals can catch problems such as premature component wear, early.
Sensors improve safety
Danger zones are identified as dangerous for many reasons. Sometimes, a technician must drive to a site to take a measurement or check on a problem. Sensors remove the threat by providing an alternative to manually taking measurements, including the need to travel to remote locations. With remote sensors in place, the data can be viewed from a distance.
Comparison – With and without sensors.
With Sensors |
Without Sensors |
Viewing real-time measurements from a distance via an app on a mobile phone or laptop |
Using a ladder to take asset measurements in a hard-to-reach area |
Trending sensor data remotely to identify a conditional change that could lead to a fault |
Manually troubleshooting equipment problems in an area with high heat, noise, or moving parts |
Using a sensor to stream data automatically to the cloud which is them accessible using a smart device |
Dispatching an employee to a remote location to measure and record data manually |
Safety saves money
A rigorous safety program can not only save lives, but it also saves money. The U.S. Occupational Safety and Health Administration Recommended Health and Safety Programs estimates that a 50-person plant that implements a strong safety and health program can typically increase productivity by 13% and save over $265,000 in defective products. Additionally, organizations that uphold a strong safety program are more attractive to job candidates when it’s apparent that the organization prioritizes safety.
Deploying sensors does not mean you can let your guard down. With automation, new types of danger zones are creeping up. Always keep your safety program up-to-date and your employees well-trained in safety best practices.
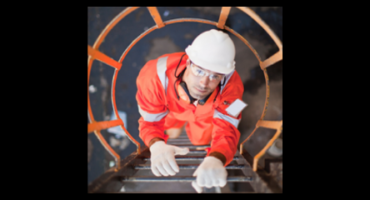
Accelix Connected Reliability Framework, Fluke Connect™ software, and sensors provide you with continuous asset measurements. Data from vibration and power monitoring sensors is uploaded to the Fluke Connect Cloud, where teams can easily access measurements on smart devices, such as mobile phones, tablets, or PC/Mac computers.
A similar post was originally published on Accelix.com.