About the Author
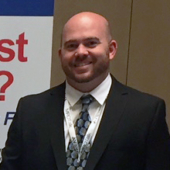
Mark Koch is a member of the Technical Support team at ALL-TEST Pro, LLC (ATP), where he has provided professional support worldwide for users of ATP equipment since 2014. He has 17 years of electrical and reliability maintenance experience. In 2001, he started his career as a construction electrician. During this time, he worked his way up from shop floor apprentice to a foreman in charge of starting and completing remodel and new construction projects. In 2010, he began working at the Metropolitan Sewer District (MSD) of Greater Cincinnati, Ohio, USA, where he learned electrical maintenance best practice and helped implement a predictive maintenance program (PdM). During his service at MSD, his team was the recipient of both the Uptime Magazine’s Best Emerging Maintenance Reliability Program Award and the Uptime Magazine’s Best Asset Condition Management Program Award. At MSD, he learned and provided routine PdM services such as thermography, vibration, lubrication, visual inspection, motor testing, and ultra-sonics.
Education and Certifications:
2001-2006- International Brotherhood of Electrical Workers (IBEW) Apprenticeship Program and the National Electrical Contractors Association (NECA) Inside Wireman Certification.
2013- PdM Visual Testing Level 2 Certification & Level 1 Thermographer Certification; 2014- Vibration Analysis Level 1T Certification.
hello
i have a question; what to do when dissipation factor is 100 %? i use the all pro test 7 for this test.
DF>100%
C=30.68 nF